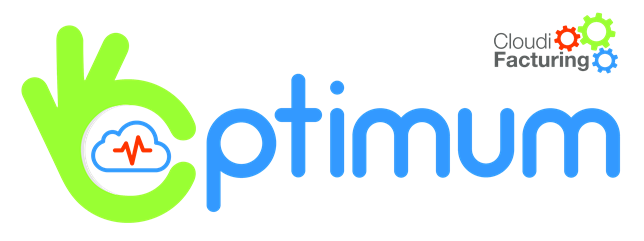
Experiment Description
Injection molding is a manufacturing process for producing parts from both thermoplastic and thermosetting plastic materials. Material is fed into a heated barrel, mixed, and forced into a mold cavity where it cools and hardens to the configuration of the cavity. The injection process it is a cyclic process, susceptible to several factors that can compromise the stability of the process and could increase the rejection rates.
The OPTIMUM experiment aims to optimise the most critical “BSI-Housing and Top” production line of GLN Plast Plant in Portugal for the production of Automotive Plastic parts and associated injection processes.
Technical Impact
Therefore, the manufacturing process will be modelled and through specific evaluation processes (using specific KPIs) and machine learning algorithms and cognitive models, it will be possible to evaluate the behaviour of the key production parameters in relation to the internal and external production variables. To this end, the PRAGMA platform will be utilized , which is equipped with trend analysis and anomalies detection modules, which will be used to detect and process malfunction diagnosis and instability together with machine learning techniques that will analyse the data stemming from the various operation of the plant to provide support for the decision of the production line manager through real-time data monitoring and data intensive visual analytics.
OPTIMUM experiment aims to cloudify data-driven and visual analytics tools for sustainable process optimization in the automotive plastic parts production, exploiting Cloud Computing by applying model-based predictive functions (available at PRAGMA platform) to the injection process. Experiment-specific machine learning models, cognitive models and optimizations techniques will be coupled with advanced visual analytics leading to cost and energy savings and improved customer-focused flexibility. Thanks to that, new knowledge will be generated to feed product differentiation and rise of software-enabled offerings for smart factories.
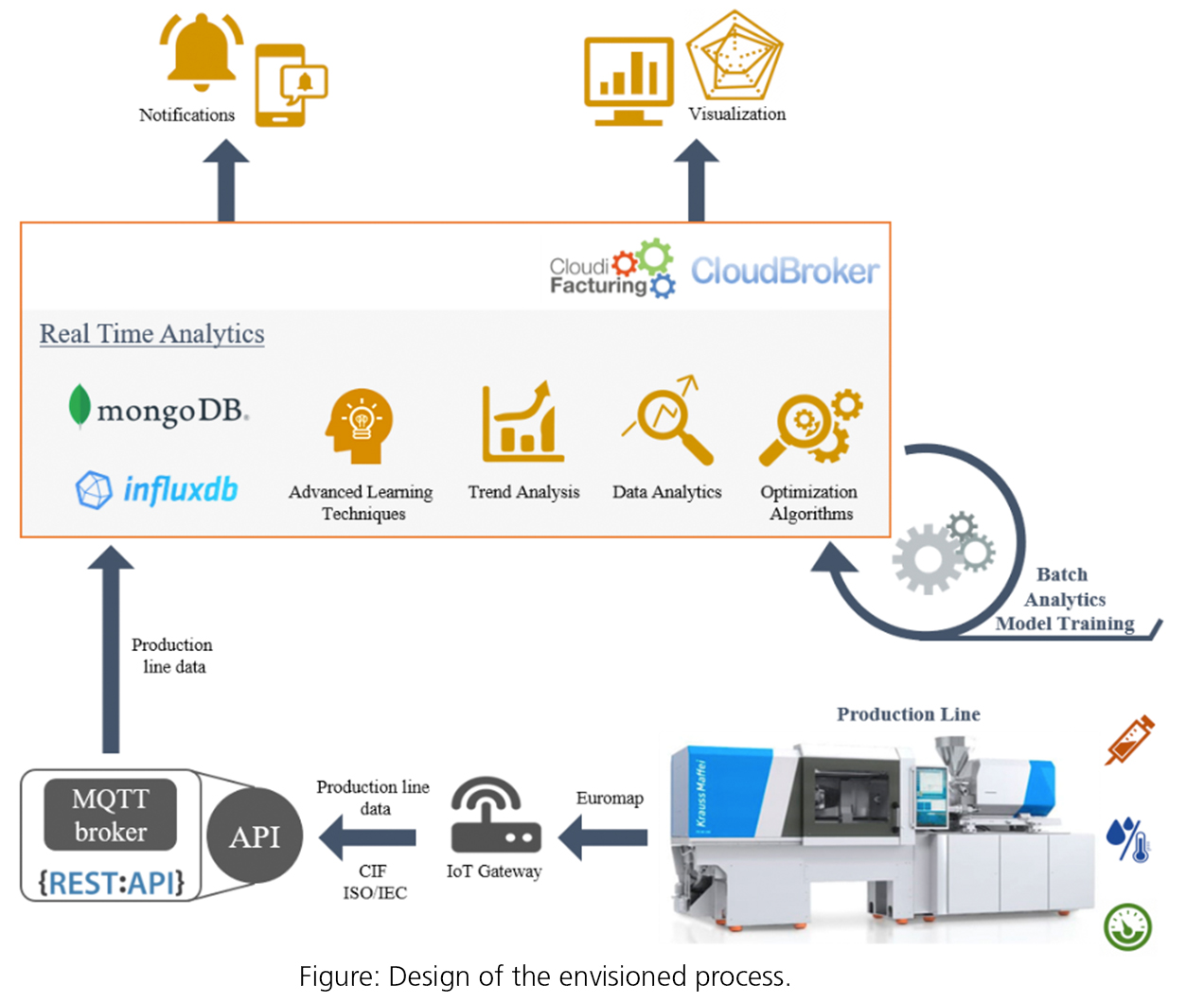
Economical Impact
Thanks to OPTIMUM, the end user will be able to identify the injection process gaps and minimize the production delays reducing the downtime of the production and the usage of the energy. Moreover, a concrete reduction of the percentage of waste parts (faulty NOK, etc.) it is expected.
Considering the possible competitive advantages deriving from the technological innovations achievable with the project activities, it is estimated that the end-user market share can increase of 200K€ per year.
Moreover, GLN Plast sees the electronic non-automotive sector as a further potential adjacent market can be intercepted thanks to technological improvements. In this market new opportunities might be created, resulting from the increased performance rates that the company is working to achieve. The project will have positive consequences on technical and economic impact of the CloudiFacturing Platform as well as the EU industry-driven strategy as a whole. GLN Plast will supply the use case needed to validate the objectives of this experiment by making available production line of GLN Plast Plant in Portugal for installing any physical support needed to evaluate PRAGMA’s trend analysis software and ML techniques and cognitive modelling to support the decision of the production line manager through real-time data monitoring and data intensive visual analytics. E@W will act as an engineering consultant and system integrator, studying together with PRAGMA how to exploit the experiment results to propose services to new potential clients.
Experiment Partners
Competence Centers
Digital Innovation Hub
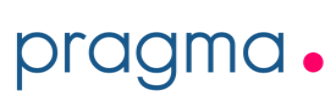
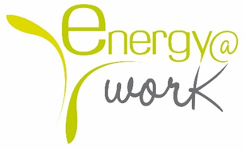
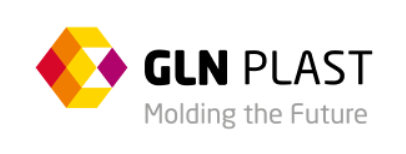


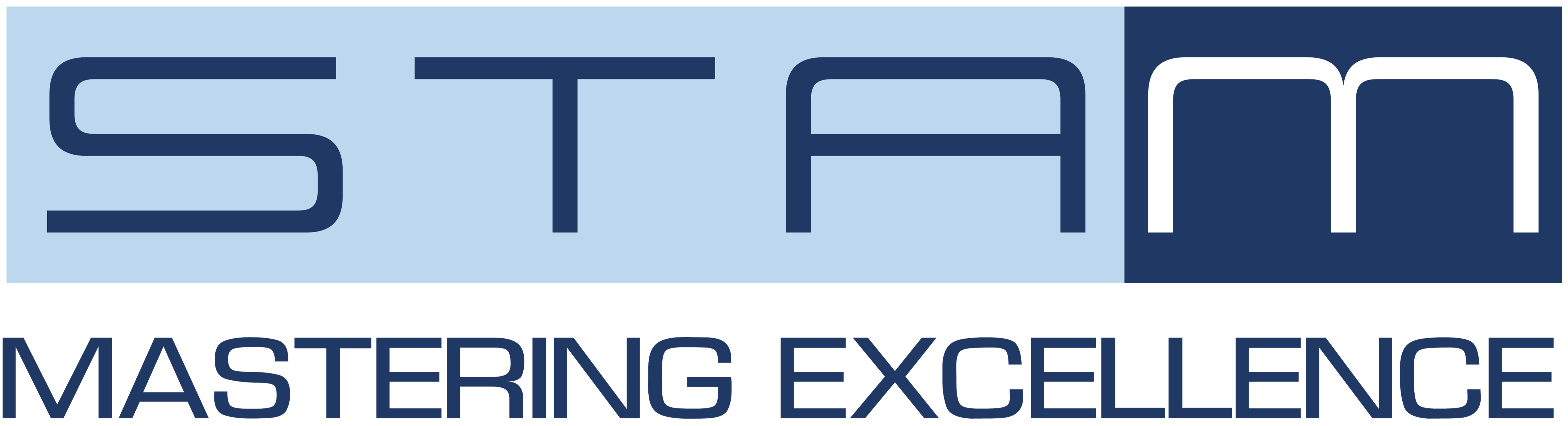