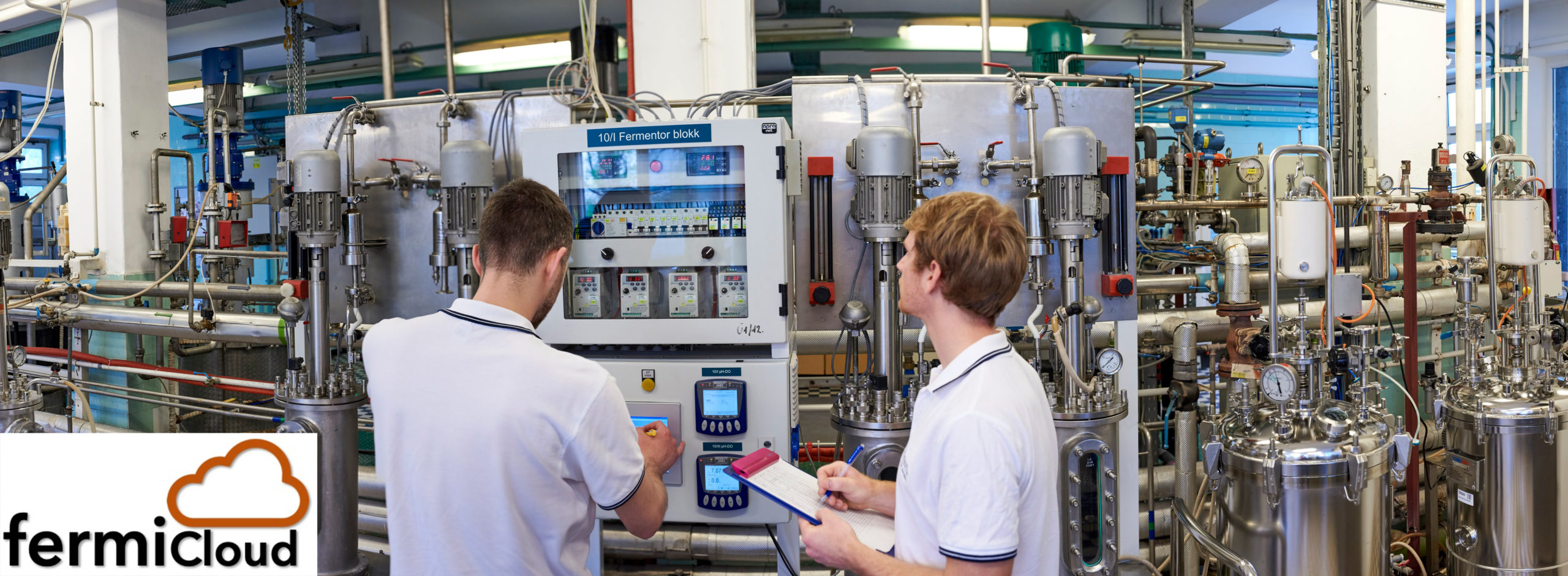
Experiment Description
Proteins, which are widely used for industrial and medical applications, are difficult or impossible to be synthesized chemically. Instead, biotechnological processes are used such as recombinant fermentation. Pichia fermentation is a highly flexible, promising method for industrial use. Despite its advances, the production remains expensive, the yields low and the risk of losing a batch is high.
Fermentia is a contract manufacturer of proteins as a final product by recombinant fermentation technology. Within this experiment the specific type of proteins production process, Pichia fermentation, was meant to be optimized. Before the FermiCloud experiment, end-user - Fermentia used manual sample analysis and corrective actions, including reagent addition, based on the results (‘As-Is’ solution). However, time dependent analysis process frequently led to low product yield or serious product loss. FermiCloud proposes a new way for bioprocess optimization via automatization as well as processing and understanding past process data.
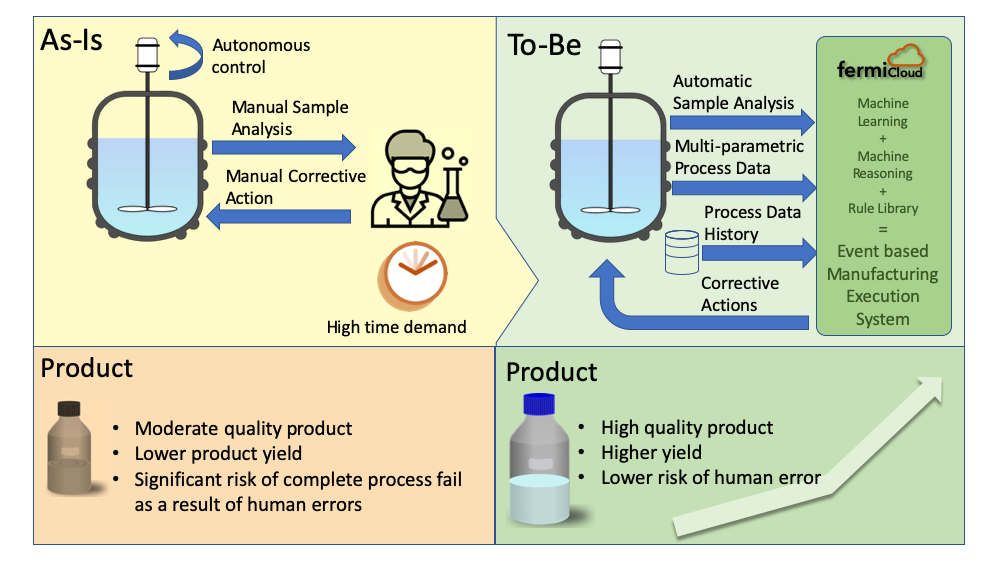
Technical Impact
This experiment approach suggested a ‘To-Be’ solution which reduces the response time of the control loop and replaces heuristic decision making by a rule library based on big data analysis, which overall leads to higher product yield and better product quality. The solution is based on data driven modelling which requires extension of the parameters space with new variables. Such parameters can be measured by advanced techniques, which previously were not available at Fermentia. Spinsplit LLC, as ISV partner, provided the necessary IoT ready fluid handling modules which enabled to perform the required chemical analysis. Moreover, ISV flagship software product SpinStudio Flow Chemistry gained capabilities of cloud connection in order to provide a machine protocol execution system for the rules obtained by the cloud based on-line process analysis. ESSI.tech supplied the partners with engineering consultancy and production of process specific sensors.
Economic Impact
All partners may mutually benefit from the CloudiFacturing project through potential growth of net income and widening of client network.
The proteins manufacturing process, based on Pichia pastoris fermentation, takes roughly a week and costs typically 30kEUR per 1000 g of protein product. Due to the uncertain process control used (“As-Is solution”) Fermentiaaccounts for 50% yield and 20% chance of completely losing a fermentation batch causing in average 3 kEUR loss per batch. Through the FermiCloud solution, losing a batch can be completely avoided, yet the product yield can be increased up to 90%.
For SpinSplit, the possibility of using the company solution (SpinStudio) together with the cloud services and the ability of the interoperability with larger scale SCADA systems may open up new markets, such as the biotechnology industry. The possibility of broadening the network of contacts will result in a higher number of new contracts and partners in new countries. That in turn will significantly increase the value of the company.
ESSI.tech was able to test the company's product (ODcube) and its software in a new, high-end application. The company was able to gather invaluable data required for the improvement of the product, which will consequently help launch the ODcube into a new market offering of CloudiFacturing compatible solutions.
Experiment Outcome
Provided by CloudiFacturing project resources allowed the experiment partners to build cloud based services and perform fermentation process control and optimization. The project managed to integrate heterogeneous elements of the system including: SCADA, cloud services, hardware control software (SpinStudio) and flow chemistry system.
During three days of trial fermentation cloud based machine learning algorithm of random forest successfully, without human intervention, performed a phase switch between the first two fermentation phases. The constant, real-time data flow between all the integrated parts of the system was kept using Apache Spark data streaming. Newly installed in Fermentia optical density sensor - ODCube governed the change between second and the third phase and gave information about health of the fermentation broth. Cloud based Manufacturing Execution System was successfully guiding the fermentation process including appropriate reagent addition and methanol level control.
The experiment resulted in enthusiastic end-user’s reception and prospect of lowering the time, which Process specialists need to devote to a single fermentation. Due to the FermiCloud solution, that time can be reduced to 17h, compared to 40h spent by Fermentia employees during the classical fermentation.

"FermiCloud gave us an opportunity to be a step ahead in a competitive market segment, by allowing our software and hardware to communicate with the cloud services. International Partners, professional project support and possibility of creating a real industrial impact - these are the key values which CloudiFacturing project supplied us with."

"One of the most complicated fermentation technologies controlled from the cloud was as big step in the life of Fermentia Ltd. as it was to land on the moon for mankind. The combination of a high degree of automation and minimal local hardware requirements has meant so far a non-existent set for us. There is no doubt about the future of Fermicloud."

"FermiCloud project allowed us to test our main product - ODcube - in a new application and integrate it into CloudiFacturing - compatible computing system. This opens new markets where our solutions and products can be applied."
Experiment Partners


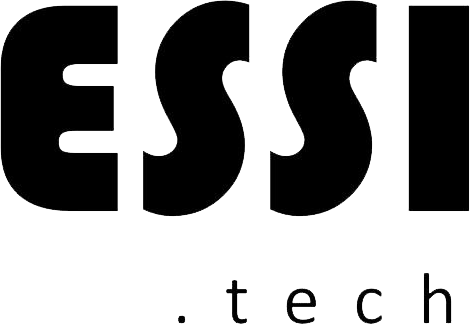
Competence Centers
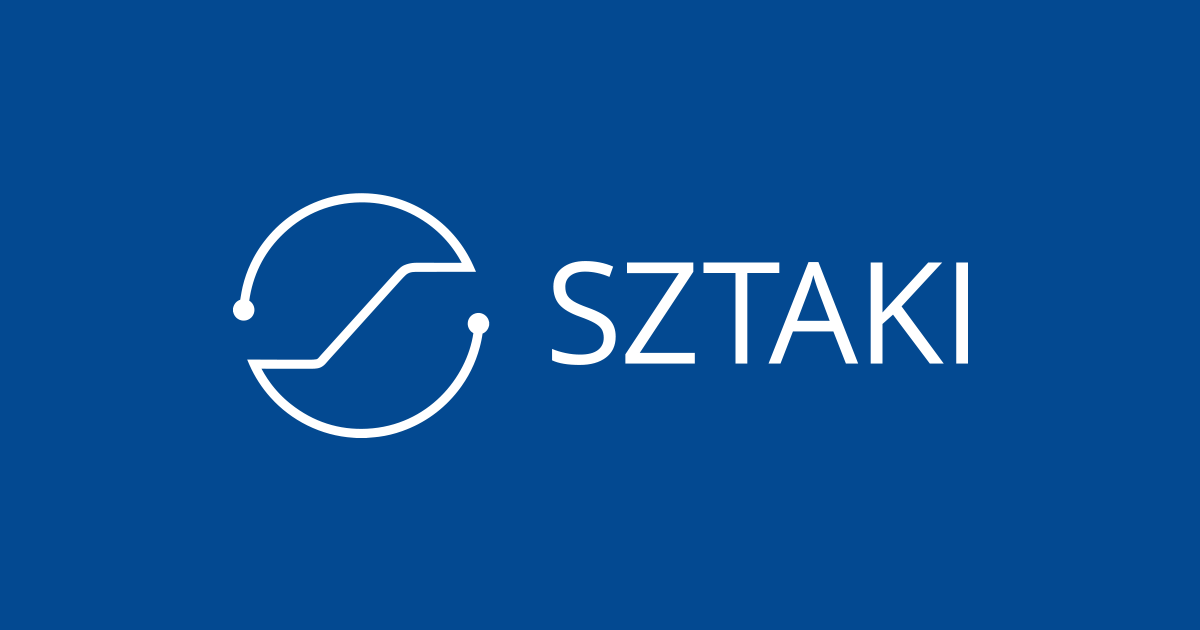
Digital Innovation Hub
