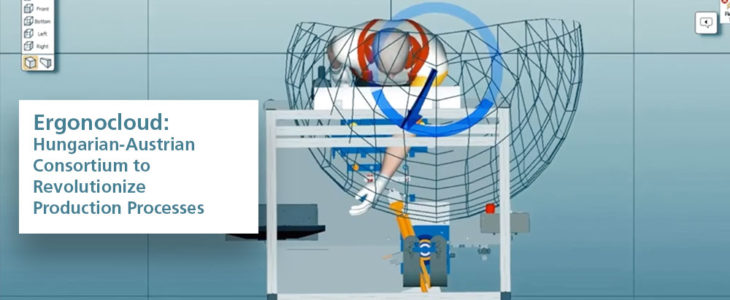
Hungarian-Austrian Consortium to Revolutionize Production Processes
The Corona pandemic has forced the slowdown or shutdown of many economic sectors, including manufacturing. The difficult times, however, also present an opportunity for companies to prepare for the post-crisis challenges and forge technological capital by digitalizing. Ergonocloud, Experiment 19 in the CloudiFacturing Project, has begun work on just such an industrial solution, supposed to make production 30 percent faster, radically more efficient, while significantly reducing on-the-job accidents.
The emergence of the coronavirus has caused grave difficulties in a number of industries and created opportunities in others: while it has boosted pharmaceutical research, it has temporarily paralyzed tourism and hospitality and put some manufacturing segments - e.g. the automotive industry - into hibernation. What can a company do if it is forced to stop or slow production? It can use the period of crisis to develop and invest in digital solutions that may provide them with a competitive advantage during the post-crisis recovery.
ErgonoCloud, which consists of a Hungarian-Austrian consortium, is working on the development of such a high-tech solution within the framework of the European Union's CloudiFacturing innovation program. In 12 months, the consortium of the Institute of Advanced Studies, Kőszeg (iASK), ViveLab Ergo Kft. and Austrian In-Vision Gmbh. They will develop a technology to improve production ergonomy, increase the efficiency of work while contributing significantly to the healthy state of mind and body of employees. The singular technology under development may assist many companies to improve the efficacy of their manufacturing processes and their working conditions.
Manufacturing Ergonomics is a Key to Digitalization
ErgonoCloud builds on ViveLab's existing solution, which increases production efficiency by optimizing production processes, reducing losses and improving quality. It achieves this by determining the position of employees in relation to machines, tools and each other during the production process, the postures they should take and movements they need to make as they perform their tasks. Digital modeling and thorough international standard evaluation of manufacturing and quality assurance is done by collecting data from sensor-equipped garments which analyze the movement of workers and the efficiency of the work process.
Data Analysis Performed by iASK
The institute is responsible for the analysis of the data both already available and newly recorded during measuring. „[…] Our world has become very intricate and complex. Processes are sometimes dizzyingly rapid, contradictory, and more and more often lead to almost indecipherable conflicts. As a research institute active in several disciplines, we consider participating in such high value-added innovation programs and putting our wide research capacities to use in the development of practical solutions very important”, says Professor Ferenc Miszlivetz, Director General of iASK. This technology has so far been used mainly in lower value-added manufacturing, such as assembly work. One of the key implications of the ErgonoCloud project is extending its application to higher value-added manufacturing processes. In addition, a cloud-based software is to be developed: all workstations will be equipped with tablets, and operators will receive instruction from and by this software on how to execute their jobs more efficiently.
This technology has so far been used mainly in lower value-added manufacturing, such as assembly work. One of the key implications of the ErgonoCloud project is extending its application to higher value-added manufacturing processes. In addition, a cloud-based software is to be developed: all workstations will be equipped with tablets, and operators will receive instruction from and by this software on how to execute their jobs more efficiently.
Innovation Funded by the European Commission
Under the CloudiFacturing program, funded by the European Commission, the consortium received a grant of one hundred thousand euros for the implementation of the project. The resource is managed by the German Fraunhofer Institute, also involved in the development as a contributing and project-oriented organization.
In Hungary, the project was supported and submitted for support by ‘innomine’ Group Kft. – who, on the domestic side, oversee the proper use of resources and the effectiveness of work processes.
“The project will be completed in one year, with the development of an Industry 4.0 product. We expect to see a product that will eventually be sold on the market. We are very optimistic, because this technology will be a major breakthrough for industry: production will be 30 percent faster, there will be fewer faulty products, accidents at work will be eliminated, and training and replacement of labor due to illness will be accelerated.” - says Gábor Vicze, Managing Director of innomine Group Kft.
Learn more about Ergonocloud Experiment
ViveLab Ergo Kft.
The founders of ViveLab Ergo Kft. have worked in Germany for three decades as an ergonomic expert and software developer. They have worked with companies such as Airbus, Daimler, Kraus Maffei and Robert Bosch, as well as developed several human simulation software. Combining valuable experience with customer needs, the cloud-based, user-friendly ViveLab Ergo simulation software was developed in 2012 to check workstation compliance based on 7 ergonomic analyses and standards based on CAD and motion files. The company professionals use the software to support the creation of an optimal work environment and workflow to increase health, efficiency, competitiveness and profitability, as well as employee health and satisfaction.
iASK
The Institute of Advanced Studies, Kőszeg (iASK) is a cross-disciplinary, interconnected scientific center focusing on research on the sustainability, economic, social and environmental challenges facing humanity. It brings together a critical mass of intellectually open, courageous and curious professionals from all over the world. While dealing with the profound problems of the future, it is also an active member of the community: it measures its activities not only by the number of publications and conferences, but also takes science to the local community and is deeply immersed in the history, culture and economic development of Western Hungary.
In-Vision
In-Vision Digital Imaging Optics GmbH develops and manufactures highly precise opto-electronic and opto-mechanic systems (“Light Engines”) for industrial applications. The company was founded in 2000. In-Vision was the first company to present a digital 4K projection lens to global markets in 2013 and has translated this experience into the development of light engines where In-Vision is currently a global technology leader.
